Apr 11, 2025
Apr 11, 2025
When Lithium Goes Astray: Understanding Lithium Plating
When Lithium Goes Astray: Understanding Lithium Plating

In our last post, we explored the Solid Electrolyte Interphase (SEI)—a crucial but complex layer that forms on the negative electrode of lithium-ion batteries. While SEI growth is an inevitable part of battery aging, another degradation mechanism can lead to even more severe consequences: lithium plating. In this post, we’ll take a closer look at lithium plating, the conditions that cause it, and how it can be modeled.
Lithium plating occurs when metallic lithium deposits on the surface of the negative electrode instead of intercalating into it. Unlike lithium ions stored within the electrode structure, plated lithium forms a separate layer that can significantly impact battery performance and safety.
Several conditions favor lithium plating:
Low temperatures: At cold temperatures, lithium-ion diffusion slows down, making it harder for lithium ions to intercalate into the electrode. If charging continues at high rates, lithium can instead accumulate as a metallic layer.
High charging currents: Fast charging pushes lithium ions into the anode rapidly. If the electrode cannot accommodate them quickly enough, plating occurs.
High state of charge (SoC): When the negative electrode is nearly full, there are fewer available sites for lithium-ion storage, increasing the likelihood of plating.
Lithium plating is problematic because it contributes to battery degradation in multiple ways: it reduces available lithium inventory, increases internal resistance, and, in severe cases, forms dendrites—needle-like lithium structures that can pierce the separator and cause short circuits, potentially leading to thermal runaway.
Lithium plating is typically modeled alongside other electrochemical processes, much like SEI growth. A plating reaction term is added to the electrochemical equations to describe how much lithium deposits on the electrode surface, and an additional equation tracks how this affects electrode porosity. There are multiple approaches to modeling this reaction:
Irreversible plating: The plated lithium is permanently lost, reducing the battery’s lithium inventory over time.
Reversible plating: Under certain conditions, plated lithium can dissolve back into the electrolyte during discharge, partially mitigating its effects.
Partially reversible plating: A combination of both behaviors, where some lithium is lost while some can still re-enter the electrochemical cycle.
Note that in these models we are assuming lithium plating to form a uniform layer. To model dendritic growth, we require more complex 3D modeling to fully capture their formation and impact on battery safety.
The interaction between lithium plating and SEI growth is crucial, and the two processes are often modeled together. Plated lithium reacts with the electrolyte, leading to additional SEI formation. This means that lithium plating does not just reduce capacity directly—it also accelerates SEI buildup, further increasing resistance and worsening performance over time.
We have now explored SEI growth and lithium plating, along with their interactions. In our next post, we will examine the third and final degradation mechanism covered in this series: mechanical degradation—the structural damage caused by repeated charging and discharging.
In our last post, we explored the Solid Electrolyte Interphase (SEI)—a crucial but complex layer that forms on the negative electrode of lithium-ion batteries. While SEI growth is an inevitable part of battery aging, another degradation mechanism can lead to even more severe consequences: lithium plating. In this post, we’ll take a closer look at lithium plating, the conditions that cause it, and how it can be modeled.
Lithium plating occurs when metallic lithium deposits on the surface of the negative electrode instead of intercalating into it. Unlike lithium ions stored within the electrode structure, plated lithium forms a separate layer that can significantly impact battery performance and safety.
Several conditions favor lithium plating:
Low temperatures: At cold temperatures, lithium-ion diffusion slows down, making it harder for lithium ions to intercalate into the electrode. If charging continues at high rates, lithium can instead accumulate as a metallic layer.
High charging currents: Fast charging pushes lithium ions into the anode rapidly. If the electrode cannot accommodate them quickly enough, plating occurs.
High state of charge (SoC): When the negative electrode is nearly full, there are fewer available sites for lithium-ion storage, increasing the likelihood of plating.
Lithium plating is problematic because it contributes to battery degradation in multiple ways: it reduces available lithium inventory, increases internal resistance, and, in severe cases, forms dendrites—needle-like lithium structures that can pierce the separator and cause short circuits, potentially leading to thermal runaway.
Lithium plating is typically modeled alongside other electrochemical processes, much like SEI growth. A plating reaction term is added to the electrochemical equations to describe how much lithium deposits on the electrode surface, and an additional equation tracks how this affects electrode porosity. There are multiple approaches to modeling this reaction:
Irreversible plating: The plated lithium is permanently lost, reducing the battery’s lithium inventory over time.
Reversible plating: Under certain conditions, plated lithium can dissolve back into the electrolyte during discharge, partially mitigating its effects.
Partially reversible plating: A combination of both behaviors, where some lithium is lost while some can still re-enter the electrochemical cycle.
Note that in these models we are assuming lithium plating to form a uniform layer. To model dendritic growth, we require more complex 3D modeling to fully capture their formation and impact on battery safety.
The interaction between lithium plating and SEI growth is crucial, and the two processes are often modeled together. Plated lithium reacts with the electrolyte, leading to additional SEI formation. This means that lithium plating does not just reduce capacity directly—it also accelerates SEI buildup, further increasing resistance and worsening performance over time.
We have now explored SEI growth and lithium plating, along with their interactions. In our next post, we will examine the third and final degradation mechanism covered in this series: mechanical degradation—the structural damage caused by repeated charging and discharging.
In our last post, we explored the Solid Electrolyte Interphase (SEI)—a crucial but complex layer that forms on the negative electrode of lithium-ion batteries. While SEI growth is an inevitable part of battery aging, another degradation mechanism can lead to even more severe consequences: lithium plating. In this post, we’ll take a closer look at lithium plating, the conditions that cause it, and how it can be modeled.
Lithium plating occurs when metallic lithium deposits on the surface of the negative electrode instead of intercalating into it. Unlike lithium ions stored within the electrode structure, plated lithium forms a separate layer that can significantly impact battery performance and safety.
Several conditions favor lithium plating:
Low temperatures: At cold temperatures, lithium-ion diffusion slows down, making it harder for lithium ions to intercalate into the electrode. If charging continues at high rates, lithium can instead accumulate as a metallic layer.
High charging currents: Fast charging pushes lithium ions into the anode rapidly. If the electrode cannot accommodate them quickly enough, plating occurs.
High state of charge (SoC): When the negative electrode is nearly full, there are fewer available sites for lithium-ion storage, increasing the likelihood of plating.
Lithium plating is problematic because it contributes to battery degradation in multiple ways: it reduces available lithium inventory, increases internal resistance, and, in severe cases, forms dendrites—needle-like lithium structures that can pierce the separator and cause short circuits, potentially leading to thermal runaway.
Lithium plating is typically modeled alongside other electrochemical processes, much like SEI growth. A plating reaction term is added to the electrochemical equations to describe how much lithium deposits on the electrode surface, and an additional equation tracks how this affects electrode porosity. There are multiple approaches to modeling this reaction:
Irreversible plating: The plated lithium is permanently lost, reducing the battery’s lithium inventory over time.
Reversible plating: Under certain conditions, plated lithium can dissolve back into the electrolyte during discharge, partially mitigating its effects.
Partially reversible plating: A combination of both behaviors, where some lithium is lost while some can still re-enter the electrochemical cycle.
Note that in these models we are assuming lithium plating to form a uniform layer. To model dendritic growth, we require more complex 3D modeling to fully capture their formation and impact on battery safety.
The interaction between lithium plating and SEI growth is crucial, and the two processes are often modeled together. Plated lithium reacts with the electrolyte, leading to additional SEI formation. This means that lithium plating does not just reduce capacity directly—it also accelerates SEI buildup, further increasing resistance and worsening performance over time.
We have now explored SEI growth and lithium plating, along with their interactions. In our next post, we will examine the third and final degradation mechanism covered in this series: mechanical degradation—the structural damage caused by repeated charging and discharging.
In our last post, we explored the Solid Electrolyte Interphase (SEI)—a crucial but complex layer that forms on the negative electrode of lithium-ion batteries. While SEI growth is an inevitable part of battery aging, another degradation mechanism can lead to even more severe consequences: lithium plating. In this post, we’ll take a closer look at lithium plating, the conditions that cause it, and how it can be modeled.
Lithium plating occurs when metallic lithium deposits on the surface of the negative electrode instead of intercalating into it. Unlike lithium ions stored within the electrode structure, plated lithium forms a separate layer that can significantly impact battery performance and safety.
Several conditions favor lithium plating:
Low temperatures: At cold temperatures, lithium-ion diffusion slows down, making it harder for lithium ions to intercalate into the electrode. If charging continues at high rates, lithium can instead accumulate as a metallic layer.
High charging currents: Fast charging pushes lithium ions into the anode rapidly. If the electrode cannot accommodate them quickly enough, plating occurs.
High state of charge (SoC): When the negative electrode is nearly full, there are fewer available sites for lithium-ion storage, increasing the likelihood of plating.
Lithium plating is problematic because it contributes to battery degradation in multiple ways: it reduces available lithium inventory, increases internal resistance, and, in severe cases, forms dendrites—needle-like lithium structures that can pierce the separator and cause short circuits, potentially leading to thermal runaway.
Lithium plating is typically modeled alongside other electrochemical processes, much like SEI growth. A plating reaction term is added to the electrochemical equations to describe how much lithium deposits on the electrode surface, and an additional equation tracks how this affects electrode porosity. There are multiple approaches to modeling this reaction:
Irreversible plating: The plated lithium is permanently lost, reducing the battery’s lithium inventory over time.
Reversible plating: Under certain conditions, plated lithium can dissolve back into the electrolyte during discharge, partially mitigating its effects.
Partially reversible plating: A combination of both behaviors, where some lithium is lost while some can still re-enter the electrochemical cycle.
Note that in these models we are assuming lithium plating to form a uniform layer. To model dendritic growth, we require more complex 3D modeling to fully capture their formation and impact on battery safety.
The interaction between lithium plating and SEI growth is crucial, and the two processes are often modeled together. Plated lithium reacts with the electrolyte, leading to additional SEI formation. This means that lithium plating does not just reduce capacity directly—it also accelerates SEI buildup, further increasing resistance and worsening performance over time.
We have now explored SEI growth and lithium plating, along with their interactions. In our next post, we will examine the third and final degradation mechanism covered in this series: mechanical degradation—the structural damage caused by repeated charging and discharging.
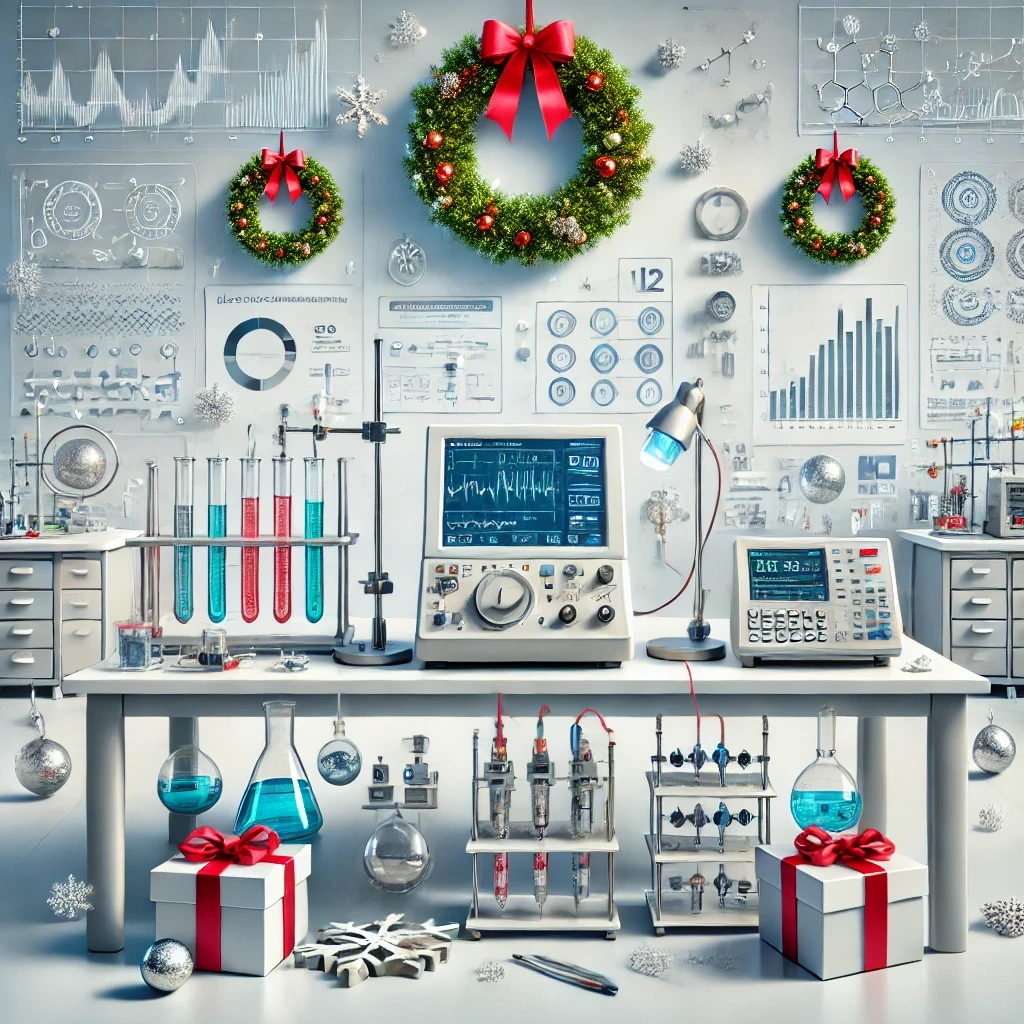
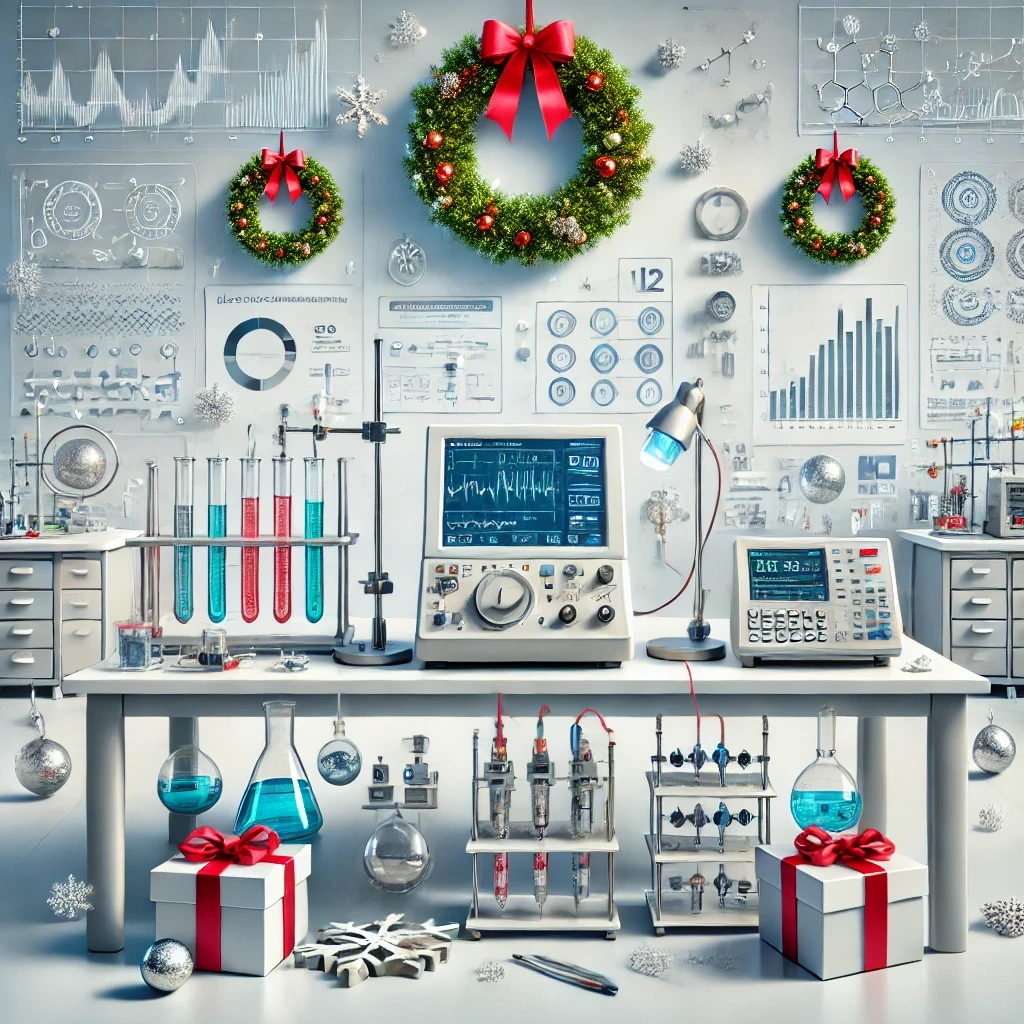
12 Days of Electrochemical Testing
To celebrate the holiday season and the re-release of Ionworks Studio, we featured "12 (business) days of electrochemical testing". Each day we pick a test, give a little bit of information about it, and show you how to run it in Ionworks. 🔋 🎄
Dec 17, 2024
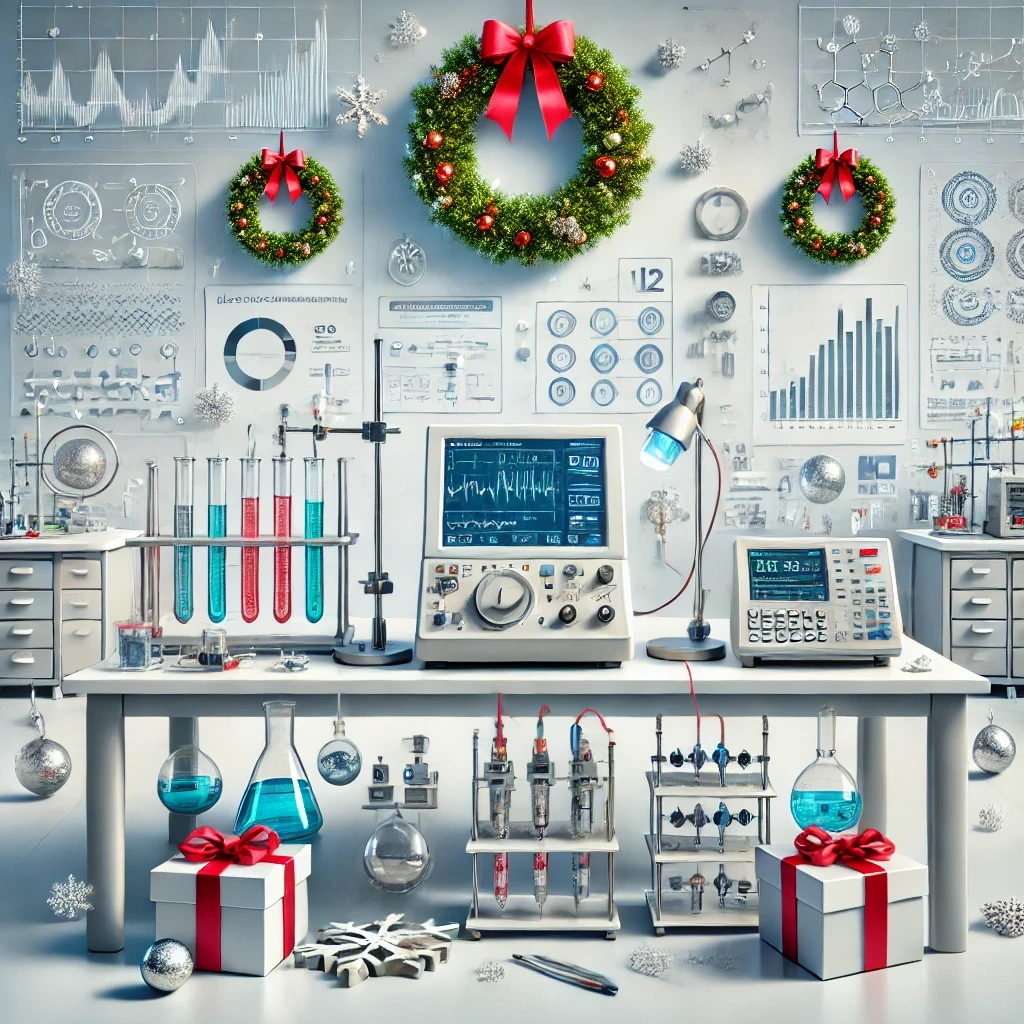
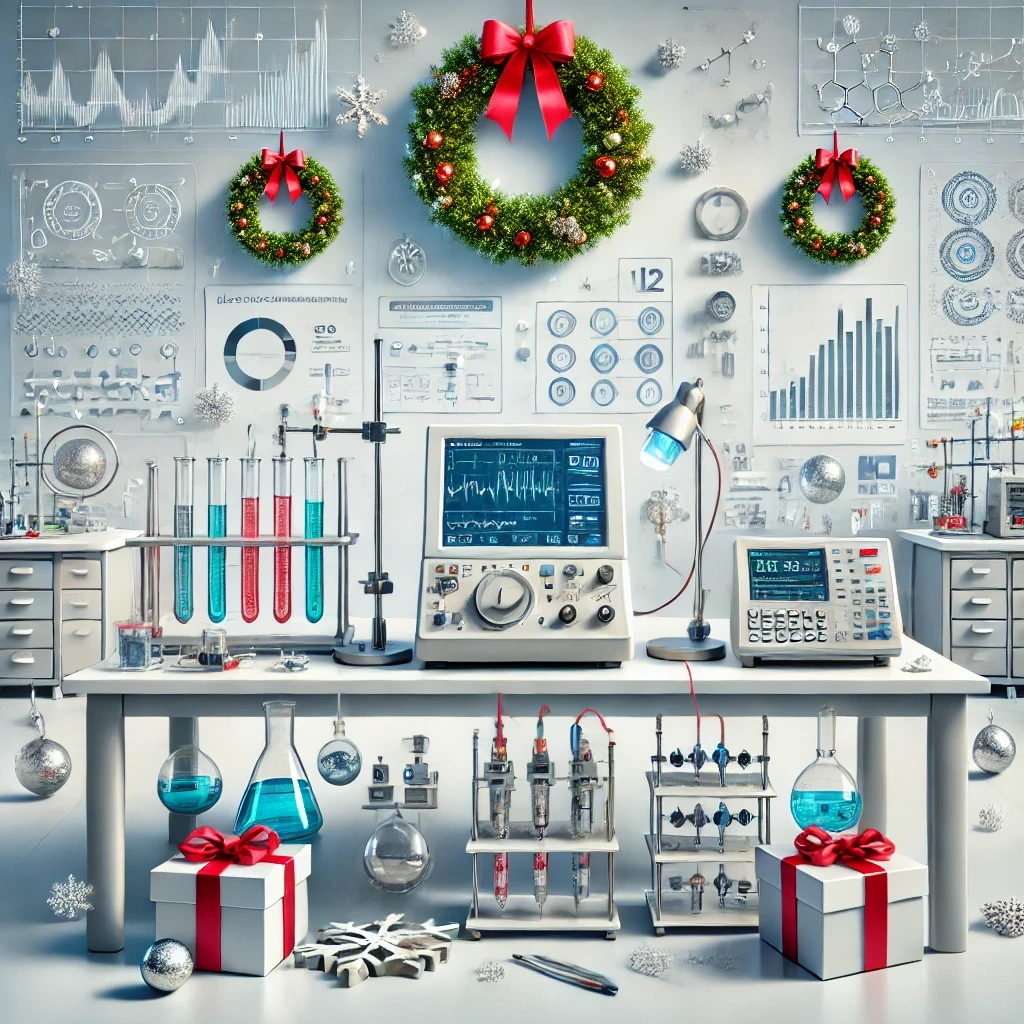
12 Days of Electrochemical Testing
To celebrate the holiday season and the re-release of Ionworks Studio, we featured "12 (business) days of electrochemical testing". Each day we pick a test, give a little bit of information about it, and show you how to run it in Ionworks. 🔋 🎄
Dec 17, 2024
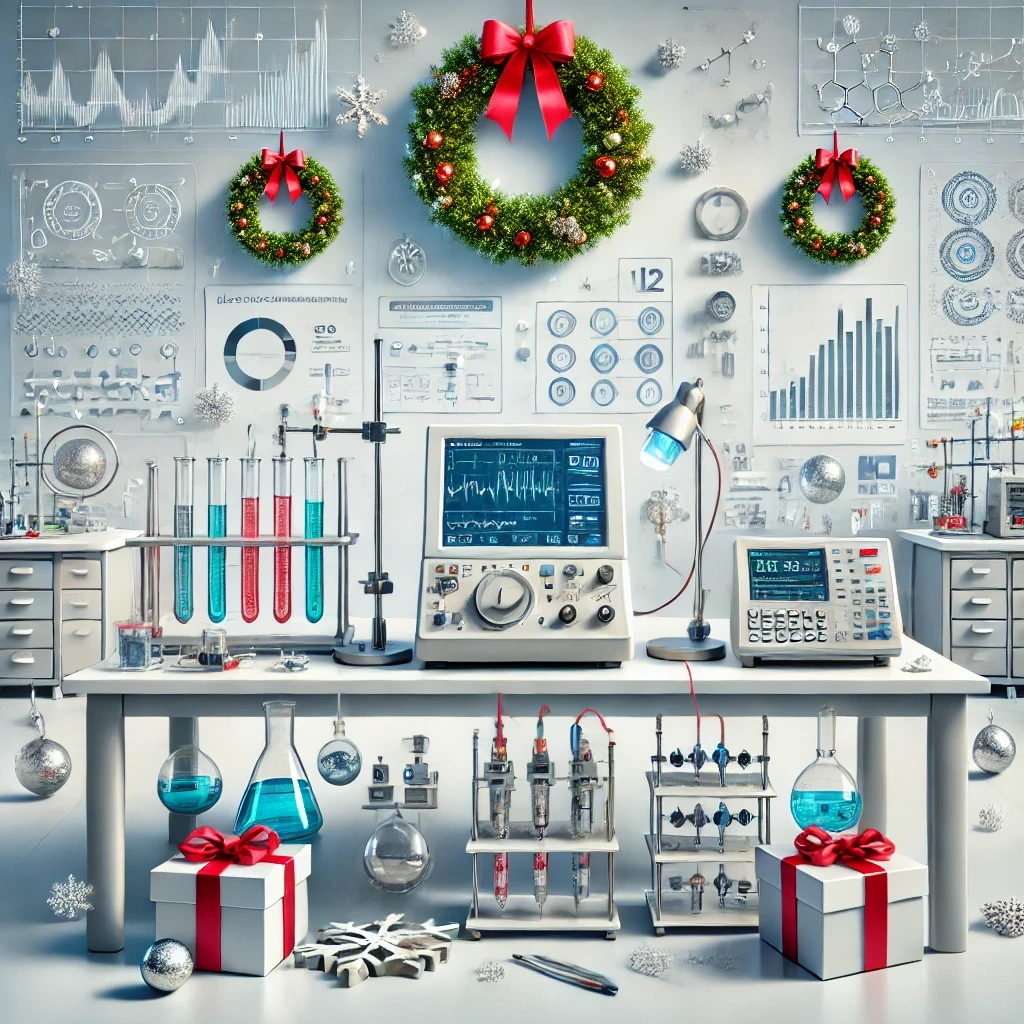
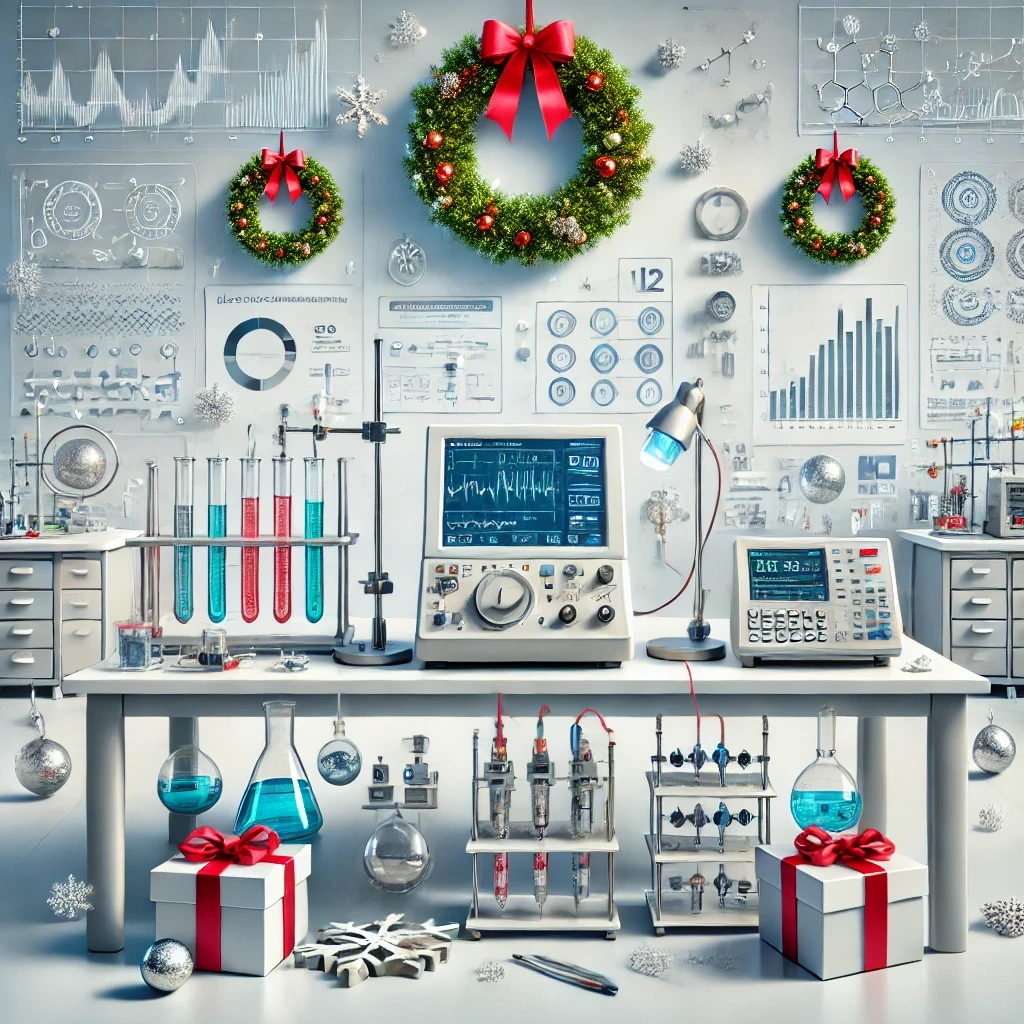
12 Days of Electrochemical Testing
To celebrate the holiday season and the re-release of Ionworks Studio, we featured "12 (business) days of electrochemical testing". Each day we pick a test, give a little bit of information about it, and show you how to run it in Ionworks. 🔋 🎄
Dec 17, 2024
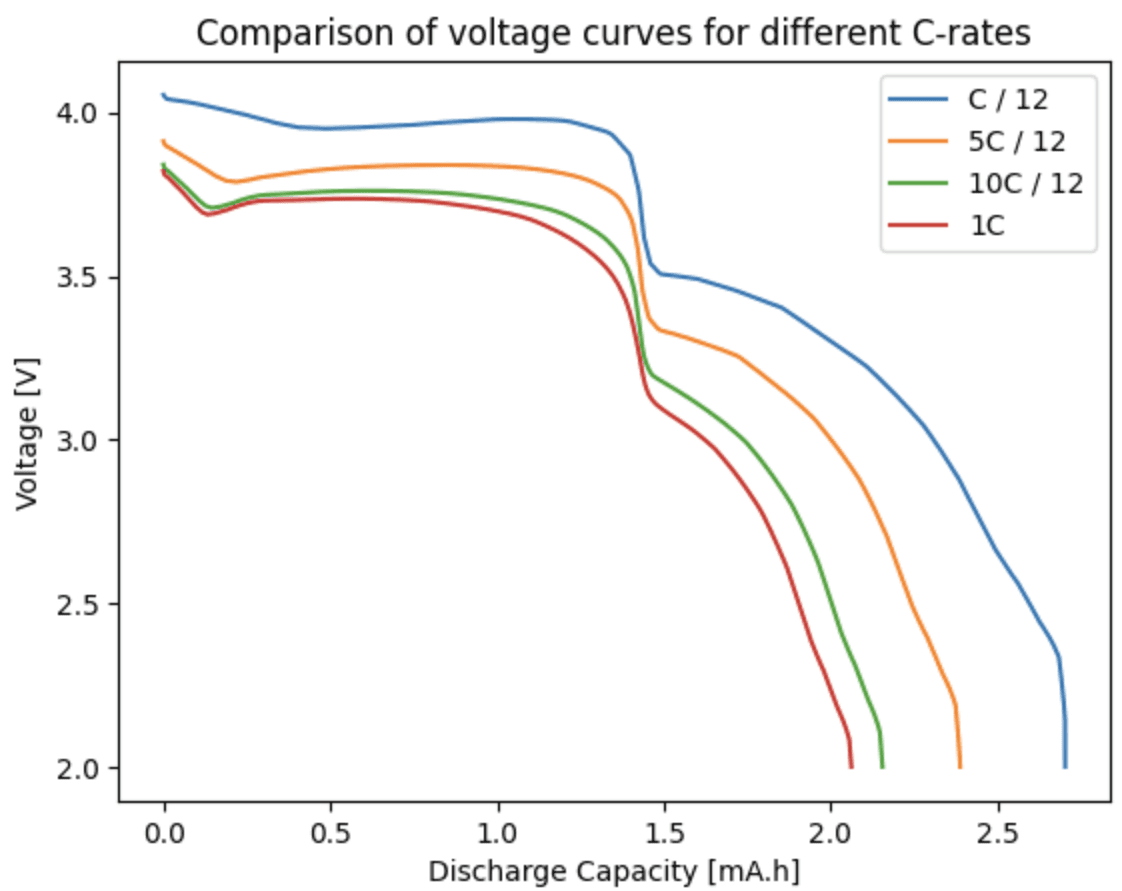
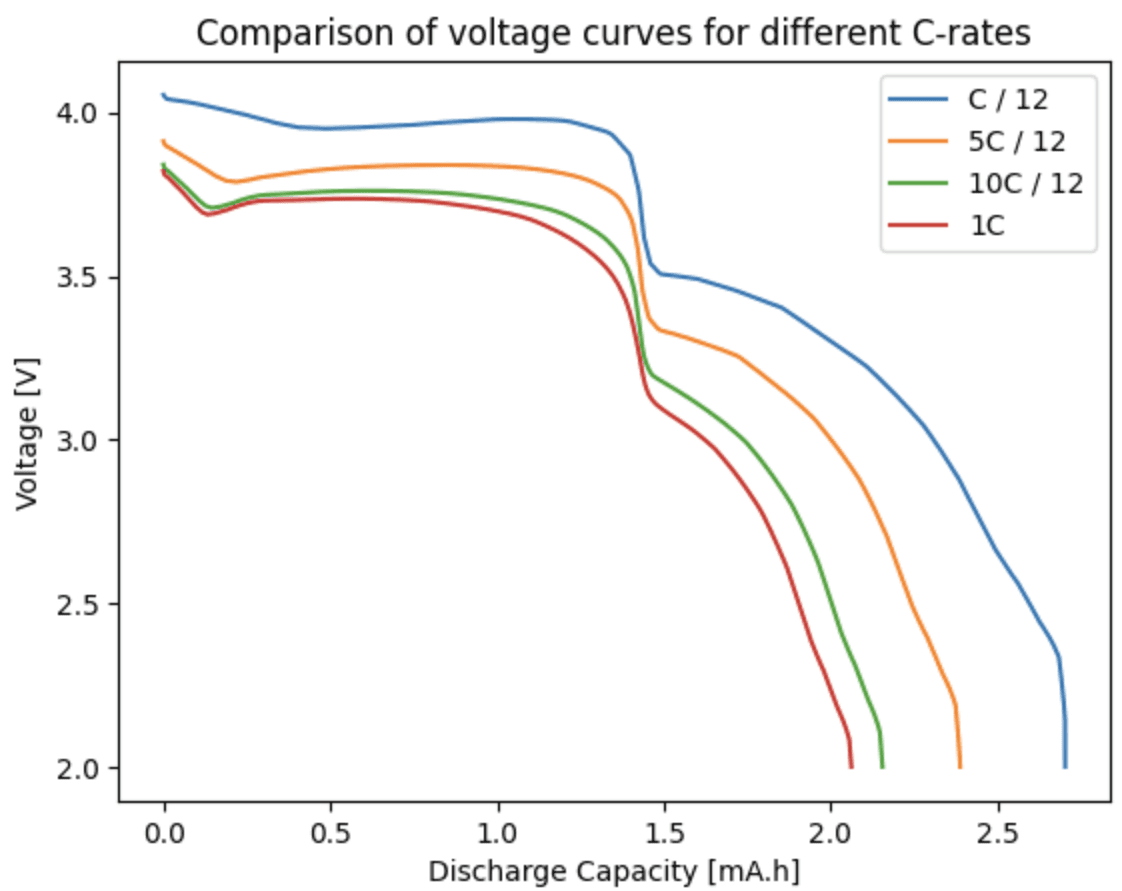
Sodium Ion Battery Model now available in PyBaMM!
This blog post explores the history of SIBs, the intricacies of the new PyBaMM model, and the exciting possibilities it unlocks for the future of energy storage.
Nov 12, 2024
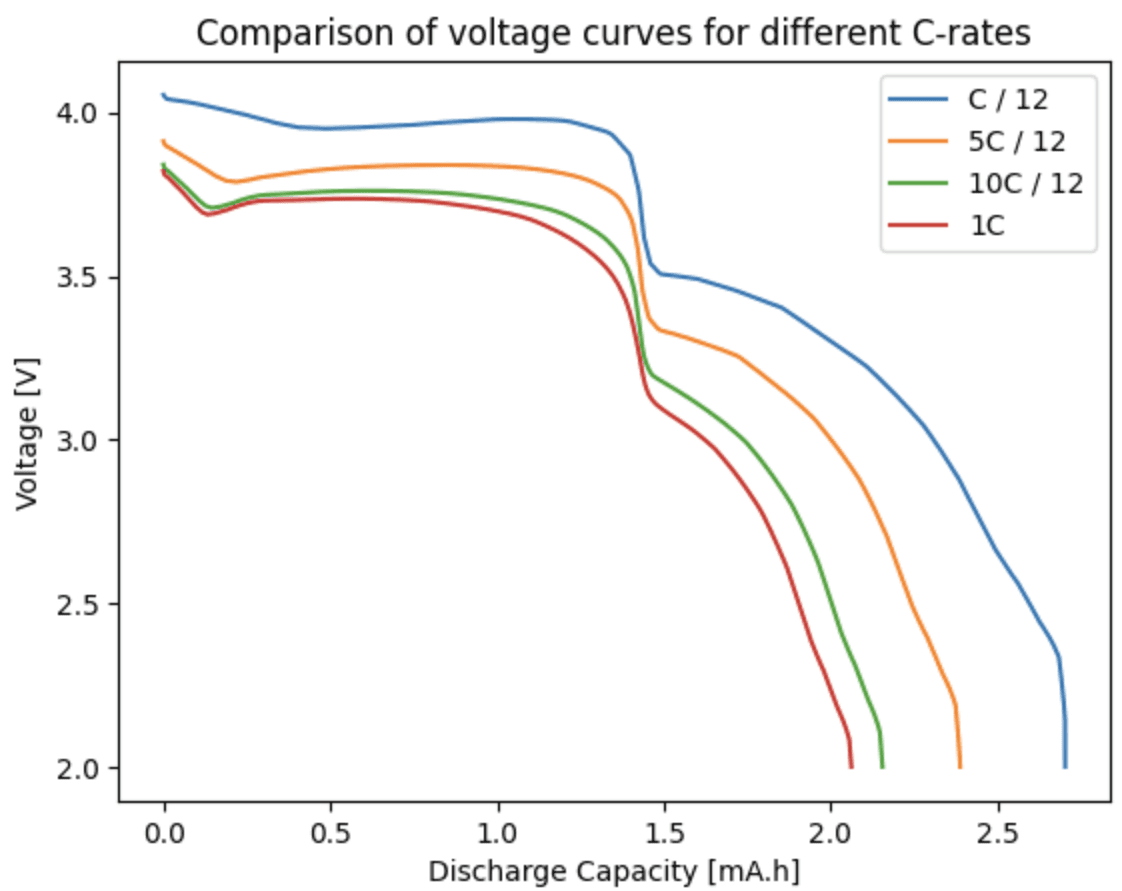
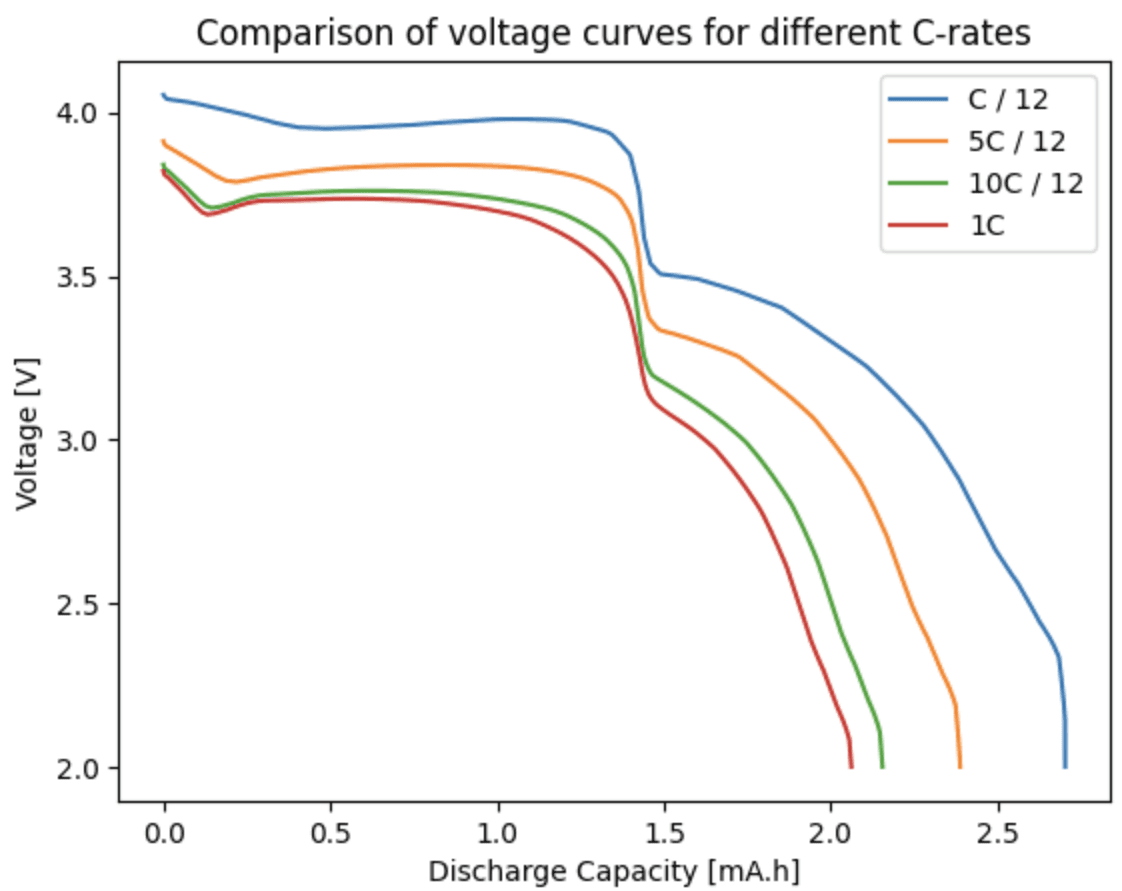
Sodium Ion Battery Model now available in PyBaMM!
This blog post explores the history of SIBs, the intricacies of the new PyBaMM model, and the exciting possibilities it unlocks for the future of energy storage.
Nov 12, 2024
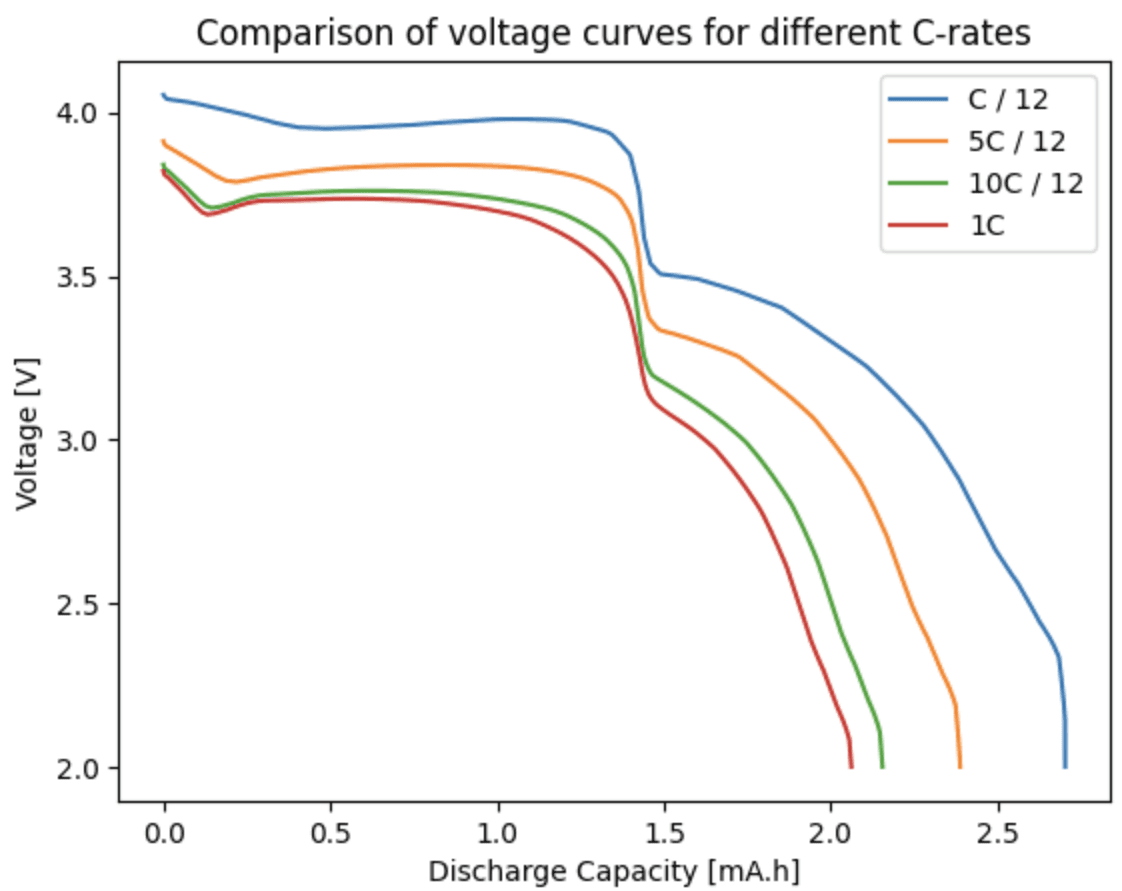
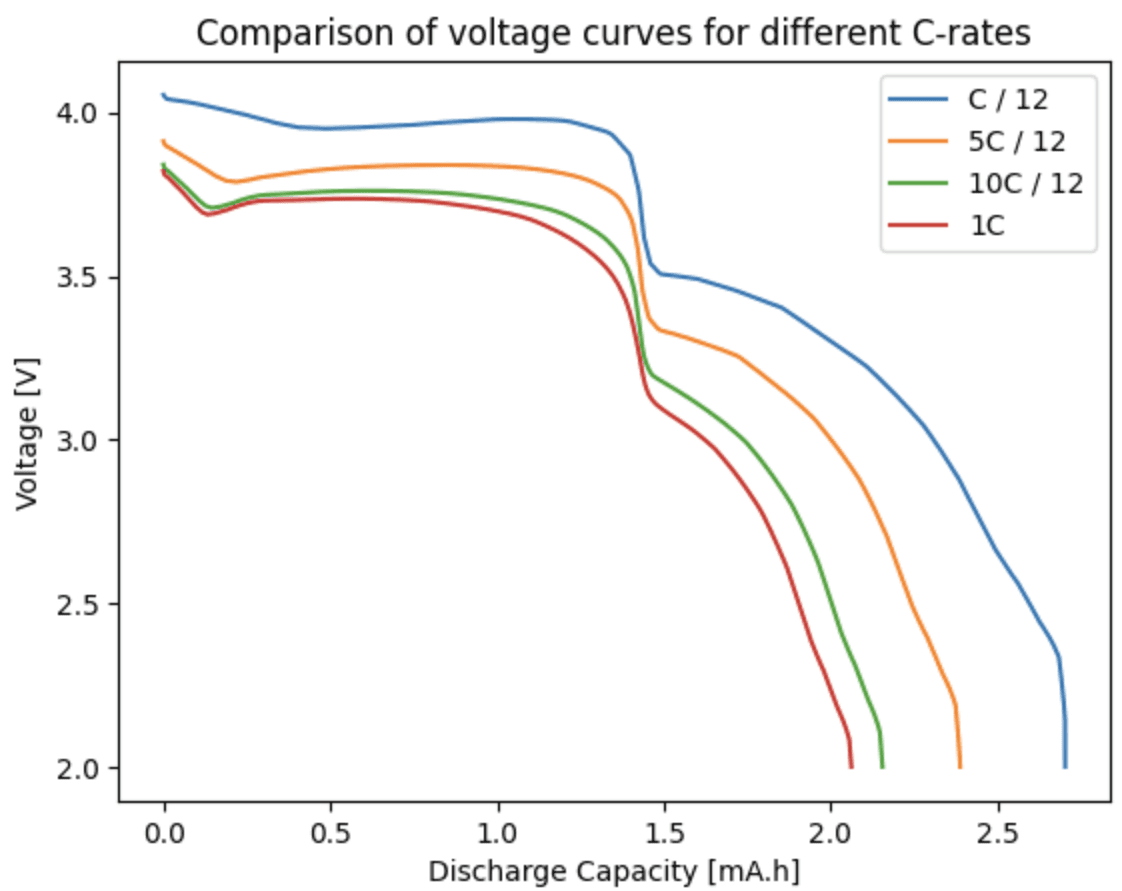
Sodium Ion Battery Model now available in PyBaMM!
This blog post explores the history of SIBs, the intricacies of the new PyBaMM model, and the exciting possibilities it unlocks for the future of energy storage.
Nov 12, 2024
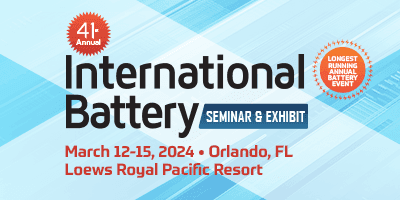
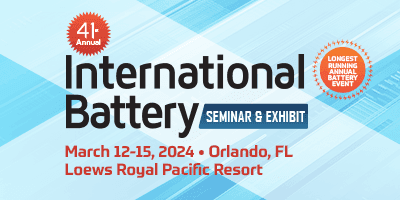
Ionworks Presents at International Battery Seminar
Ionworks CEO Valentin Sulzer presents at the International Battery Seminar in Florida
Mar 12, 2024
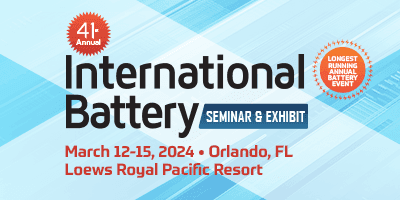
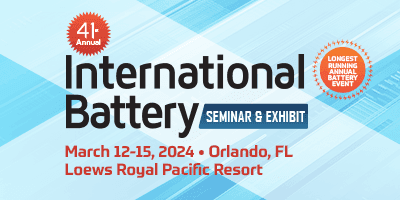
Ionworks Presents at International Battery Seminar
Ionworks CEO Valentin Sulzer presents at the International Battery Seminar in Florida
Mar 12, 2024
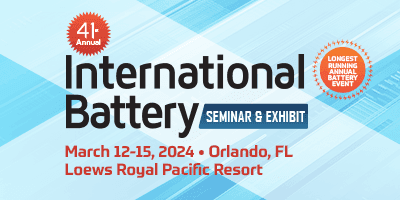
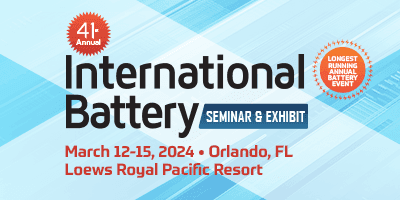
Ionworks Presents at International Battery Seminar
Ionworks CEO Valentin Sulzer presents at the International Battery Seminar in Florida
Mar 12, 2024
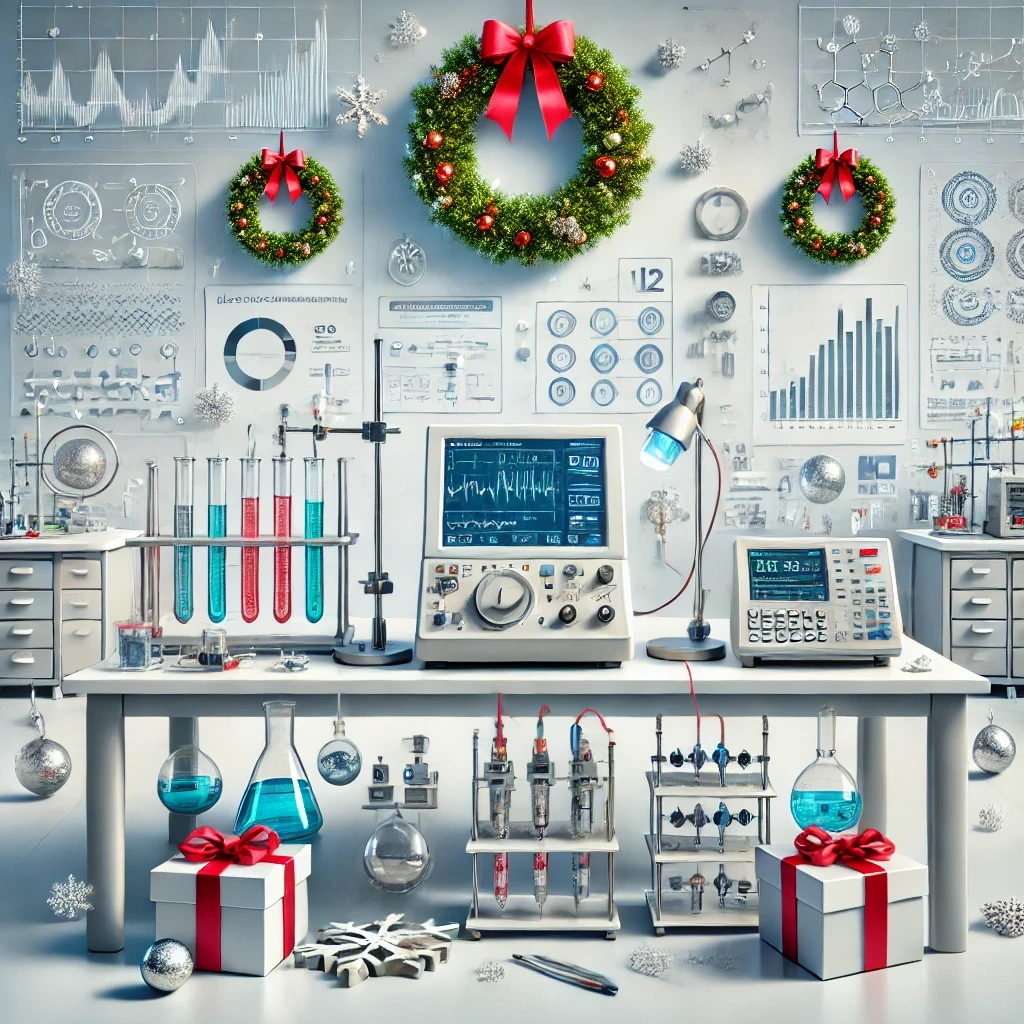
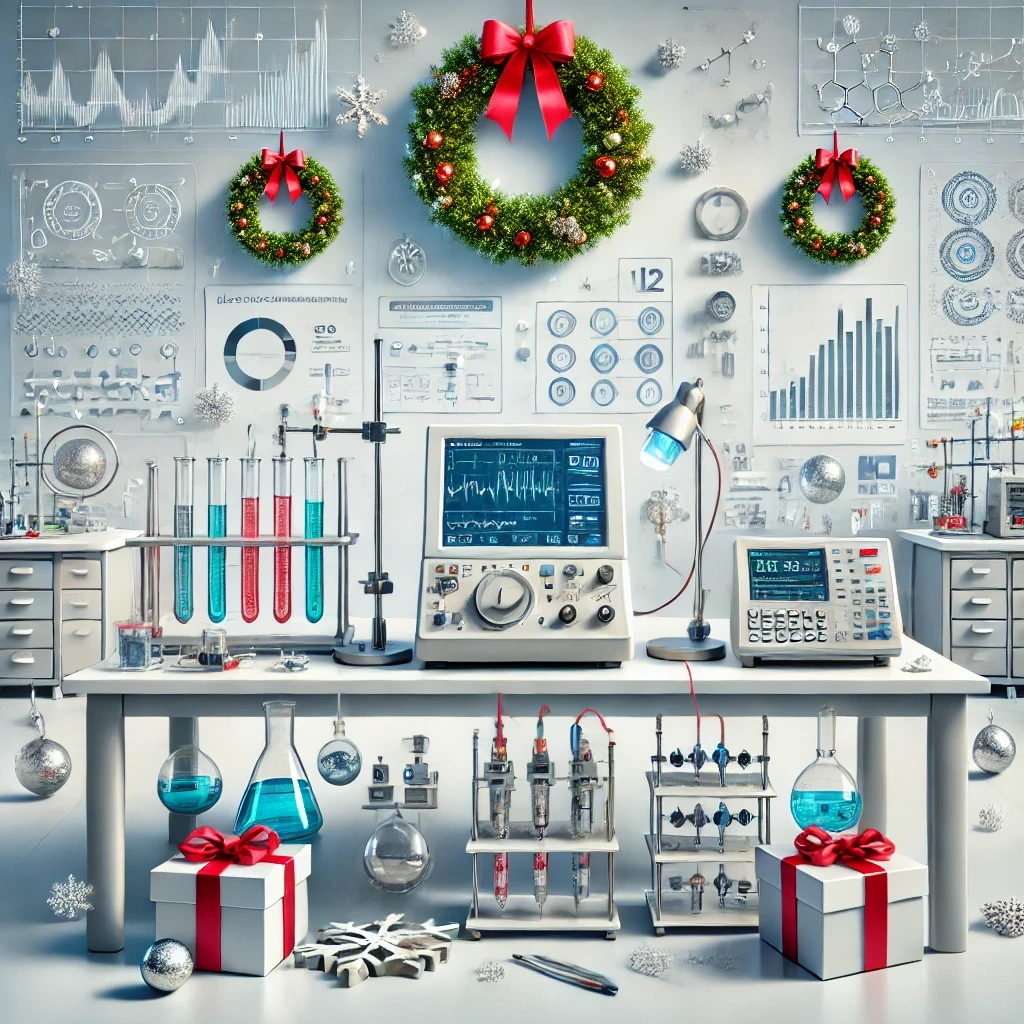
12 Days of Electrochemical Testing
To celebrate the holiday season and the re-release of Ionworks Studio, we featured "12 (business) days of electrochemical testing". Each day we pick a test, give a little bit of information about it, and show you how to run it in Ionworks. 🔋 🎄
Dec 17, 2024
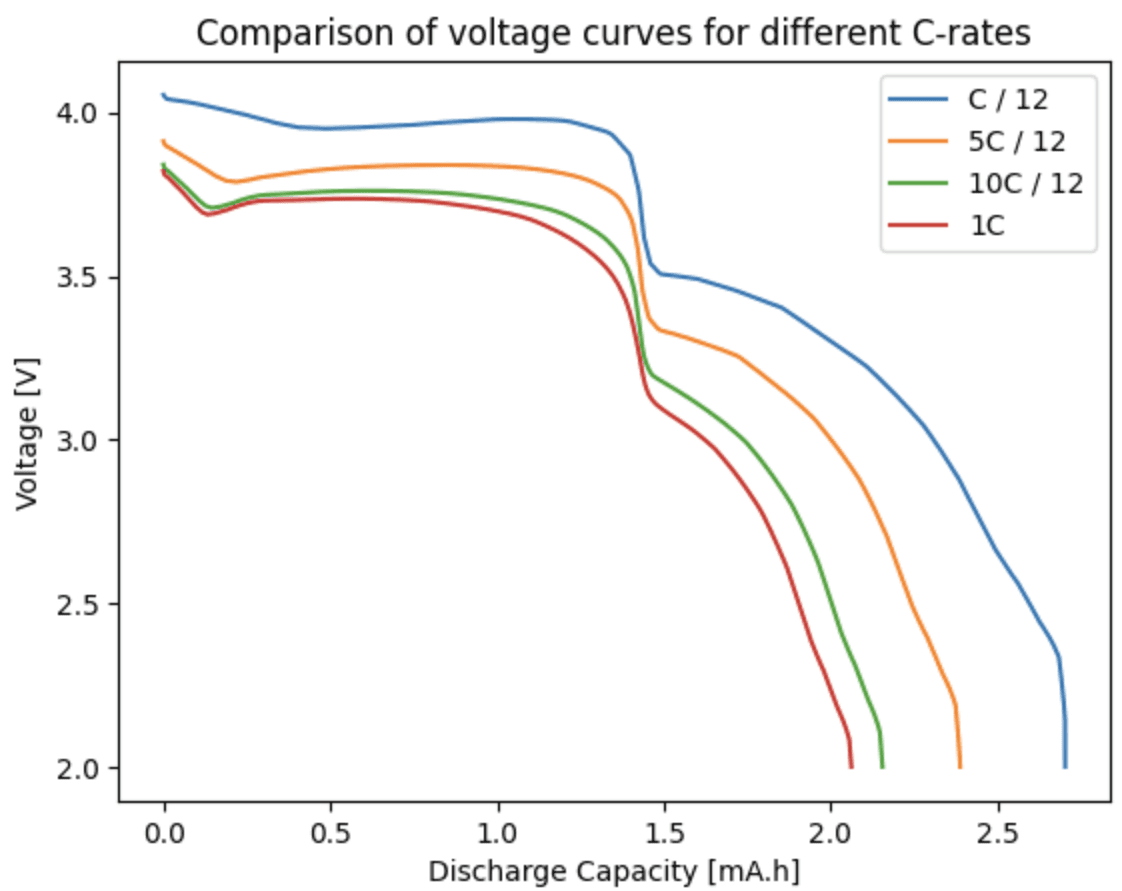
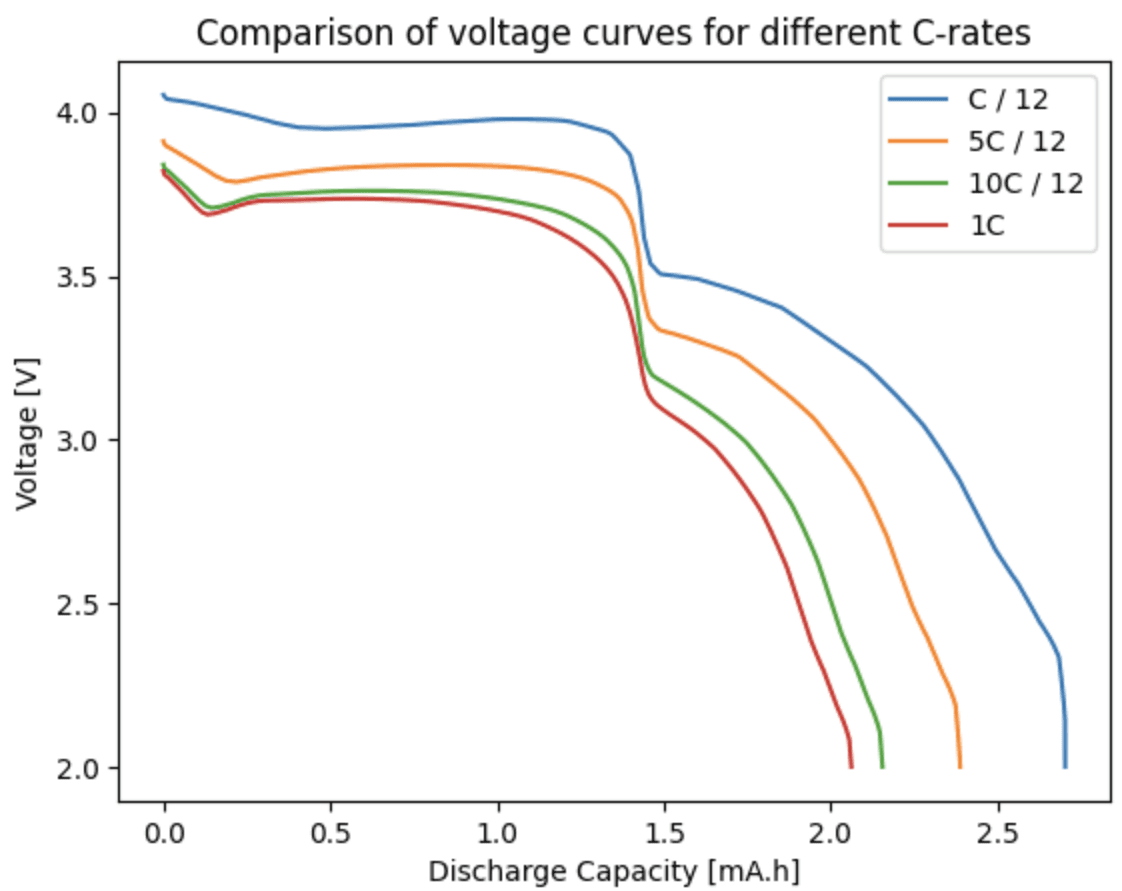
Sodium Ion Battery Model now available in PyBaMM!
This blog post explores the history of SIBs, the intricacies of the new PyBaMM model, and the exciting possibilities it unlocks for the future of energy storage.
Nov 12, 2024
Run your first virtual battery test today
Simulate, iterate, and validate your cell configurations with no lab time required.
Ionworks Technologies Inc. All rights reserved.
Run your first virtual battery test today
Simulate, iterate, and validate your cell configurations with no lab time required.
Run your first virtual battery test today
Simulate, iterate, and validate your cell configurations with no lab time required.
Ionworks Technologies Inc. All rights reserved.
Run your first virtual battery test today
Simulate, iterate, and validate your cell configurations with no lab time required.
Ionworks Technologies Inc. All rights reserved.